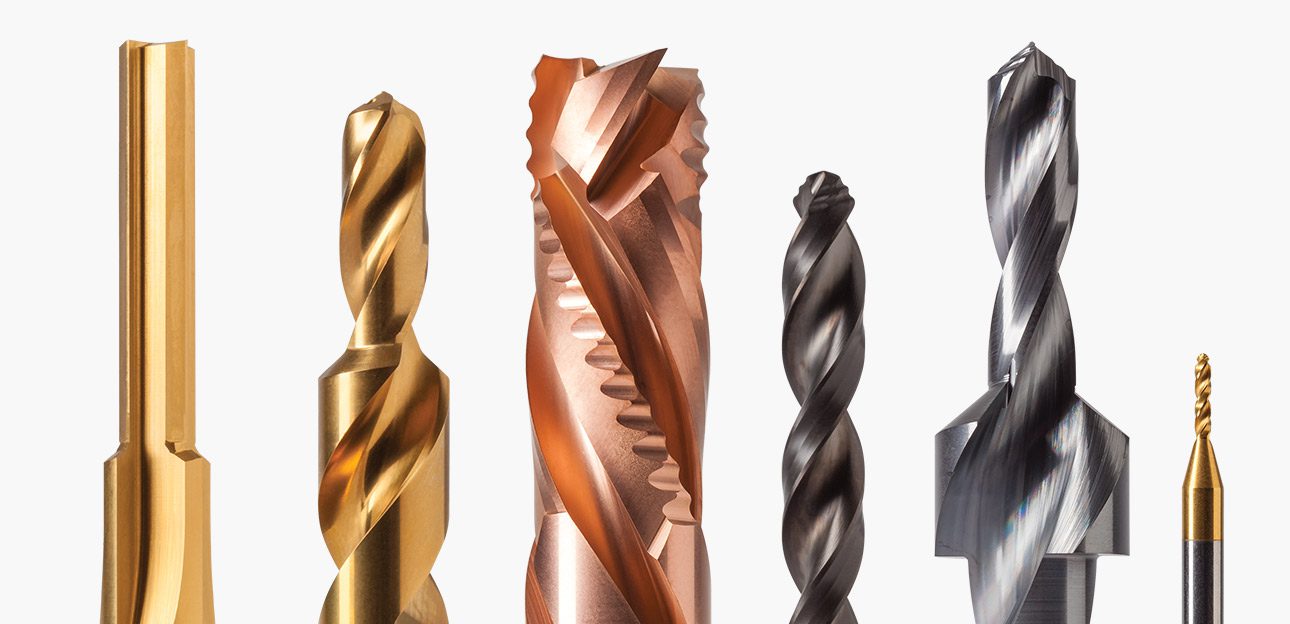
From Boeing to Airbus to Ford & GE, the world’s leading OEMs and their suppliers rely on Sharon-Cutwell.
Leverage our drill engineers and advanced manufacturing processes to tackle your toughest drilling challenges. We’ll help you design and execute complex hole-making and routing processes – delivering the throughput and tool life you need without sacrificing precision or hole quality.
Drilling and routing composites, composite stacks, and other exotic materials often present your biggest challenges for automated drilling units. We’ve got the engineering talent, tools, and experience to tackle them. From our patented Wave-Point™ technology to custom manufacturing processes developed by our in-house designers and engineers, Sharon-Cutwell provides the solutions you need to get the results you require.
The Total Cutwell Solution:
- Customers get direct access to our tooling engineering team for design & concept development.
- Cutwell Process Development Center supports special tooling R&D projects & uses the latest drilling technology.
- Dedicated in-house CNC machines.
- Utilize latest coatings to extend tool life & increase performance.
- State-of-the-Art CNC 5-axis grinders manufacture exceptionally high quality, solid carbide tooling for automated drills.
- Advanced automation & robotics provide flexibility to run both large and small jobs.
- An extremely skilled team of CNC grinder machinists – average tenure of 12+ years.
- Fast-track expediting services available.
- Full engineering support throughout tool test.
- Speeds/feeds recommendations & on-site support during testing.
- Direct engagement with engineering for any needed changes/adjustments.
- Easy access to engineering & production teams for improvements/modifications that might be needed.
- Continued communication with direct sales & engineering to ensure consistent tool life and a robust machining process.
What Our Customers Have to Say
“Sharon-Cutwell has been our go-to resource for custom tooling. They have been extremely responsive to our needs and their quality is second to none.”
“I was in a bind, so I reached out to Cutwell looking for some custom carbide woodruff cutters, in a very short turn around. They were able to quote and design the tools within 24 hours, and offer me an expedited lead time to help me hit my turnkey runoff deadline, in a few short weeks.”
“Sharon-Cutwell has supported my team as we launched the drilling and assembly of our advanced composite 777X wing. It is their desire to provide truly innovative solutions and commitment to helping us solve our challenging problems that helped us be ready on day 1.”
“I was struggling with a difficult taper reamer application on our brake knuckle launch. I searched everywhere and couldn’t find someone who could solve it until Sharon-Cutwell developed an innovative solution that was very easy for me to implement. Now it works flawlessly!”
“We really appreciate the continuous learning attitude, drive for improvements, willingness to constantly increase your knowledgebase, thru the pushing of the envelope of our product.”
Need Help with a Specific Project?
Use the form below to let us know about your project or schedule a consultation call today.
CASE STUDY:
High Performance Composite Drilling for Boeing 787
Boeing produces the largest and most advanced commercial aircraft in the world. In order to reduce weight, they utilize large amounts of composite materials. On the 787, the majority of the primary structure is made from composites. Boeing was in search of a drill manufacturer to help them solve tool life and throughput issues in composite drilling during the final assembly of the 787’s body join.
Download Our Case Study to See How We Helped Boeing
CASE STUDY:
High Performance Composite Drilling for Boeing 787
Boeing produces the largest and most advanced commercial aircraft in the world. In order to reduce weight, they utilize large amounts of composite materials. On the 787, the majority of the primary structure is made from composites. Boeing was in search of a drill manufacturer to help them solve tool life and throughput issues in composite drilling during the final assembly of the 787’s body join.
Download Our Case Study to See How We Helped Boeing